The Importance of Mould Maintenance and Repair
Written by admin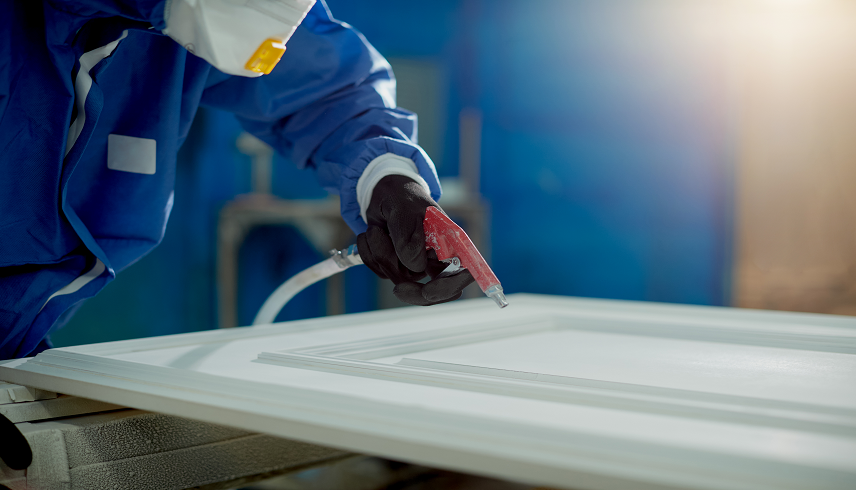
Moulds are fundamental to manufacturing processes, especially in industries like plastics, automotive, and consumer goods, where precision and repeatability are essential. Moulds are responsible for shaping raw materials into finished products, making them vital in ensuring consistent quality across production runs. However, given their constant use under extreme conditions, moulds are subjected to wear and tear, which can degrade their performance over time. This makes mould maintenance and repair critical to ensuring high-quality production, minimising downtime, and prolonging the lifespan of the moulds. A well-maintained mould not only guarantees that parts meet the required specifications but also reduces the chances of defects, which can lead to costly rework, downtime, and lost profits.
Neglecting mould maintenance can lead to frequent breakdowns, risking production schedules and leading to unscheduled downtime, which significantly impacts manufacturing efficiency. Additionally, regular maintenance helps extend the lifespan of the mould, thereby saving companies from the high costs associated with mould replacement. The significance of routine maintenance cannot be overstated as it directly affects production quality, cost-effectiveness, and the overall efficiency of the manufacturing process.
Consequences of Neglecting Mould Maintenance
Neglecting mould maintenance can result in several detrimental consequences that disrupt production and inflate costs. One of the most significant impacts is a reduction in part quality. Defects such as flash, sink marks, or dimensional inaccuracies can become common when a mould is not properly maintained, leading to substandard products that may need to be scrapped or reworked, increasing waste and cost. Production downtime is another consequence, as poorly maintained moulds are more likely to break down unexpectedly, causing unscheduled stops in production. This downtime can severely disrupt manufacturing schedules and delay deliveries, resulting in financial losses and strained customer relationships. Furthermore, frequent breakdowns lead to increased costs, as more resources are required for urgent repairs. Over time, these costs add up, often surpassing the expense of regular maintenance. In extreme cases, moulds may need to be replaced altogether, which is an even more costly endeavour. Finally, neglecting maintenance shortens the lifespan of moulds. Without routine care, moulds wear out faster, necessitating premature replacements that further strain the budget and reduce operational efficiency.
Types of Mould Maintenance
To avoid these negative consequences, mould maintenance should be prioritised. There are several types of maintenance strategies that manufacturers can employ:
- Preventive Maintenance: This involves regularly scheduled inspections, cleaning, and minor adjustments to keep moulds functioning optimally. The goal is to prevent unexpected failures by addressing issues before they become problematic.
Predictive Maintenance: This method uses data and condition-monitoring tools to predict when maintenance will be required, based on the mould’s performance. By tracking wear and tear, manufacturers can schedule maintenance just before a breakdown occurs, minimising downtime.
Corrective Maintenance: This is reactive maintenance, carried out after a mould fails or is damaged during production. Corrective maintenance typically involves repairs or part replacements to restore the mould to working condition.
Key Components of Mould Maintenance
Effective mould maintenance focuses on several critical components that ensure the mould’s longevity and optimal performance. Cleaning is one of the most essential aspects, as it prevents the buildup of residue that can degrade materials and cause defects in the final product. Residue from raw materials or lubricants can accumulate on mould surfaces, leading to imperfections if left unchecked. Proper cleaning keeps these surfaces pristine and reduces the risk of contamination. Lubrication is another key element, especially for the mould’s moving parts, such as guide pins and slides. Regular lubrication prevents excessive wear caused by friction and ensures that the mould operates smoothly throughout production. Additionally, routine inspection is vital to catch any signs of wear, cracks, or deformations in components like cavities, cores, ejector pins, and cooling channels. Identifying and addressing these issues early on helps avoid more severe damage and prolongs the mould’s service life. Alignment checks are also crucial to ensure that the mould halves and other critical components are properly aligned, as misalignment can lead to parting line defects or dimensional inconsistencies in the finished product. By focusing on these key maintenance components, manufacturers can ensure the reliability and efficiency of their moulds.
Common Mould Repairs
Despite regular maintenance, moulds can still experience damage that necessitates repairs. One common issue is cavity damage, where scratches, dents, or wear in the mould cavity can affect product quality. These imperfections often result in surface defects in the finished parts, making it essential to repair the cavity to restore its smoothness and precision. Worn-out ejector pins are another frequent issue, as these components are responsible for smoothly ejecting parts from the mould. Over time, they can wear down, leading to difficulties in part ejection and potentially damaging the products. Replacing these worn pins is critical to maintaining the efficiency of the production process. Cracks in the mould base or other components also pose a serious problem, often resulting from repeated stress or material fatigue. If not repaired promptly, these cracks can expand and lead to more extensive damage, potentially requiring complete mould replacement. Hot runner systems, commonly used in more advanced moulds, also require attention. Components such as nozzles and heating elements can wear out or malfunction, necessitating repairs to maintain efficient material flow and prevent production delays. Addressing these common repairs ensures that moulds remain functional and continue to produce high-quality parts efficiently.
Technologies Aiding Mould Maintenance
Advances in technology have made it easier for manufacturers to monitor and maintain their moulds more effectively:
3D Scanning: 3D scanning technology enables precision inspection of moulds, allowing manufacturers to detect wear and damage with high accuracy. Scanning can reveal even the smallest imperfections, making it a valuable tool for preventive and predictive maintenance.
Condition Monitoring Sensors: Sensors that monitor critical parameters such as temperature, pressure, and vibration can provide real-time data on mould performance. This information allows manufacturers to detect anomalies early and schedule maintenance before a failure occurs, thus avoiding unexpected downtime.
Computerised Maintenance Management Systems (CMMS): CMMS tools help manufacturers schedule, track, and manage maintenance activities more efficiently. These systems can keep records of previous repairs, track inventory for replacement parts, and even predict when maintenance will be required based on the mould’s usage history.
Conclusion: Prioritising Mould Maintenance for Optimal Production Efficiency
In conclusion, the importance of mould maintenance and repair in manufacturing cannot be overstated. A well-maintained mould not only ensures the consistent quality of parts but also minimises costly downtime and prolongs the lifespan of the mould. By regularly inspecting, cleaning, lubricating, and repairing moulds, manufacturers can avoid defects, reduce production delays, and lower the overall costs associated with frequent repairs or mould replacement.
In today’s competitive manufacturing environment, maximising efficiency is paramount. Investing in preventive, predictive, and corrective maintenance strategies ensures that moulds remain in optimal condition, supporting long-term production goals. With advancements in technology like 3D scanning and CMMS, manufacturers now have more tools than ever to maintain mould performance. Ultimately, prioritising mould maintenance enhances both day-to-day operations and long-term profitability, making it an indispensable practice for any manufacturing facility striving for excellence.